Osborn - Reshoring the Right Way to Lower Costs, Improve Quality and Keep U.S. Jobs
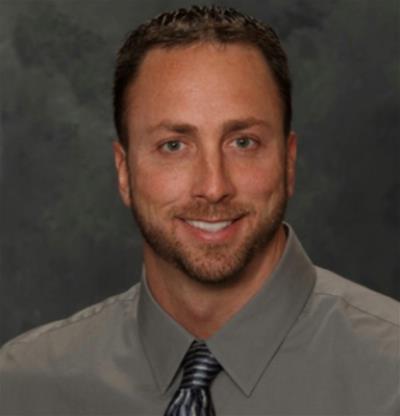
In the past 18 months, we invested $2.2 million in manufacturing automation and other equipment and systems that enhance performance, capacity and quality. The investment by Osborn is unique and will enable us to remain the world’s largest surface treatment and finishing provider.
Automation Increases Efficiency
Much of our investment went toward an automated, high-volume twist knot (TK) machine. The TK machine enhances production of twist knot Powerbrushes including our stringer beads with Osborn’s Staggered and Offset Trim patented technology, which efficiently balances cutting performance and long wire life -- something the market has never seen. With our new patented technology our stringer beads last twice as long and remove 60 percent more material than other competitor brushes in the market.
We wouldn’t be able to make the brushes efficiently without the automated system. The innovative, automated technology Osborn developed enables us to rapidly assemble wire sections and base components and press them together. That’s one of the successes of our reshoring effort. Another is how investment in the TK auto machine has made it possible for Osborn to reduce costs by as much as 50 percent.
Improving Safety and Quality
Returning twisted wire brush manufacturing to the United States also makes it possible for Osborn to enhance the safety of our products.
The automated TK machine accurately detects potential defects during or after assembly. The benefit is huge. Our brushes are used at high rates of speed. A brush component failure would be hazardous to our customers’ equipment, products and their employees. We’re better able to minimize the risks due to the advanced monitoring system integrated into the TK machine. One improvement through the advanced monitoring process is that the pressing of components is better controlled. The new TK machine generates a measured and repeatable force during final assembly. That enables consistent quality over thousands of brushes produced.
With our advanced automated assembly process and monitoring system, our internal defect rate is much lower, and the final product is much safer for the end user.
And to provide customization options and shorten lead times, the automated TK machine replaces stamping of product information with laser engraving. Now, branding, safety information and directions in multiple languages can all be quickly added and changed when ever needed. Previously, updating stamping tooling at Chinese suppliers could take months.
Realizing Our Return on Investment
Reshoring is right for Osborn, because we can deliver twist knot brushes to our customers in North America faster than we could by manufacturing the products in China. Many customers value the shorter lead time; many also believe that only an American-made product can deliver the highest quality at the right price for their needs. We agree. That’s why we brought production back to the United States. Reshoring enables Osborn to significantly reduce our cost profile. Customers benefit because we’ve enhanced quality and accelerated delivery — and can offer twisted wire brushes made in the U.S.A. at market-competitive prices.
Adding the new automated TK machine did not eliminate any jobs as often happens when other manufacturers automate workflow. In fact, with our expanded manufacturing capabilities, Osborn is winning new business. As we have added new business, we have hired more employees at our Richmond, Indiana facility.
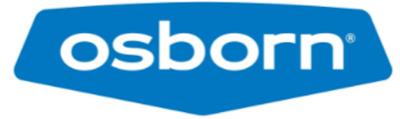
Brian Keiser | Vice President, Industrial Tools - Osborn
For more information about Osborn, please click the company name link below:
Related Articles
Osborn Parent Jason Group Rebounds To Strong 2021 Results
18/02/2022
Archived -
Osborn Tufbrush - The Toughest in the Industry
01/02/2022
Archived -
Osborn Optimises its Best-Selling Cutting Disc
16/11/2021
Archived -
Osborn Hires New CEO to Lead Next Stage of Company Growth
28/02/2021
Archived -
Osborn Parent Company Jason Industries Acquires Schaffner Mfg Co Inc
05/04/2019
Archived -
ATB® Disc Brushes with Abrasive High-Tech Bristles from OSBORN
09/05/2018
Archived -
Osborn Announces Scott Scheider as Product Marketing Manager, Load Runners®
28/02/2017
Archived -
America Takes Flight with Osborn
15/02/2017
Archived -
Osborn Introduces New Abrasives Product Line
22/08/2016
Archived -
Osborn Announces Ty Weber as Product Manager, Abrasives
14/07/2016
Archived -
Osborn Introduces New Product Catalog
17/06/2016
Archived -
Osborn Announces Engagement of Kevin Pearson
13/11/2015
Archived -
Osborn Announces Engagement of André Pelletier
13/11/2015
Archived -