Brush Expert Visits the New Hillbrush Site
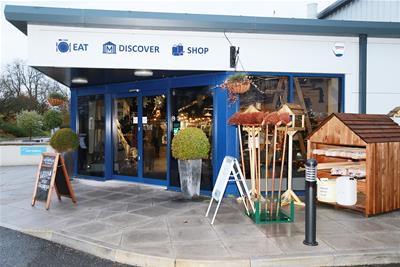
Arriving at Hillbrush, the first thing that strikes you other than the impressive scale of the site, is that the not-inconsiderable car park was packed full and it soon became clear why. Having approached Hillbrush from the busy A303, which is the major route for traffic coming into the region, it is hard to miss the large road sign inviting you to take a break from driving and Visit Hillbrush: A visitor centre combining a restaurant, shop and museum all under one roof situated directly alongside the factory, offices and warehouses.
Not only was the expansion the talk of the brush industry, but we had also heard from non-brush friends who had done exactly as the sign suggested and broken their journey with an unplanned rest stop at Visit Hillbrush. They were left with sated appetites and a newfound enthusiasm for brushes!
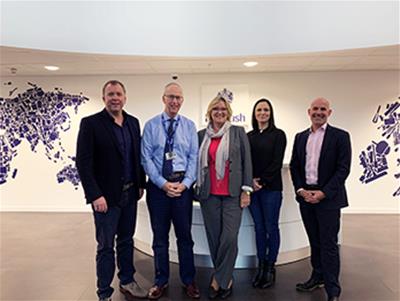
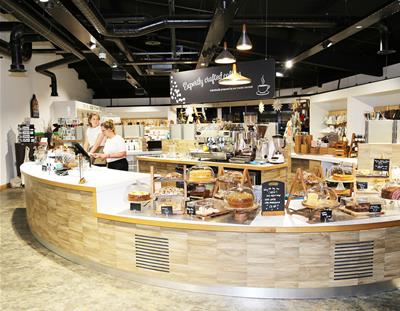
With a range of over 2000 products that are distributed to more than 90 countries across the globe, the Hillbrush factory is a busy enterprise, but we were fortunate enough that Philip Coward found the time to show us around. It’s not every day that you get a tour with the Chairman and we were particularly grateful in this instance, as Philip has intimate knowledge of the machinery and processes used to drive the business forward, having started his Hillbrush career working on the factory floor.
Traditional / Commercial Brushes
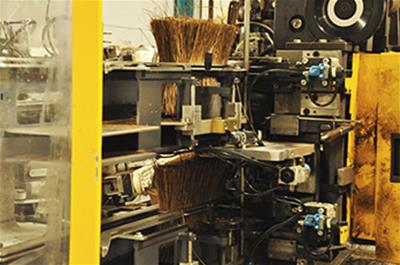
Using sustainably sourced materials including high-grade timbers and natural fibres, Hillbrush produces the majority of its traditional brushware at the Mere site. Modern robotic brush-making machinery, including custom-built lines designed especially for Hillbrush, are used to complete most tasks, with highly skilled operatives ensuring that exceptional standards are maintained at all stages of production.
The brooms and brushes fabricated in this department are grouped according to their quality bracket and budget range: Finest, Trade and Contract. This makes ordering easy, with customers able to easily identify the most suitable product group for their requirements.
In 1981, Hillbrush was granted a Royal Warrant as a mark of acknowledgement for supplying its products of high order to Royal Households. As one of 850 Royal Warrant holders, Hillbrush is entitled to use the title and Royal Arms. The Royal Warrant status products have been specially selected for their durability and effectiveness and are also available for purchase by its non-Royal customers.
Philip told us that despite the traditional side of the business continuing to flourish with a 9% increase in sales year-on-year to the domestic market, the biggest area of growth continues to be exports to the hygiene markets, focussing on production of food and beverage.
Natural fibres
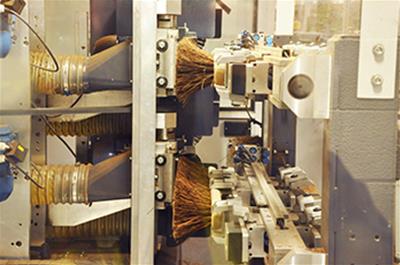
Hillbrush Hygiene
Nowadays, Hillbrush is most known for its internationally recognised Hillbrush Hygiene brand of hygienic cleaning equipment. Using pioneering technology, Hillbrush manufactures a world-class range of high-performance brushes, squeegees and other cleaning equipment.
Philip explained to us that the Hillbrush Hygiene range is one of the most advanced in the world and includes products available in 12 colours to aid colour-coding. Its Resin-Set Dual Retention System (DRS®) is one of a number of advanced solutions that set Hillbrush apart from its competitors, using anti-microbial epoxy resin to set the filaments in the brushes/brooms to eliminate the risk of filament loss and to prevent a build-up of dirt in the holes. The process is such a close-guarded secret that unfortunately we were not able to view the production room – indeed, even new employees are excluded until they have passed their 6-month probation period!
The Hillbrush MDX range of hand brushes and plastic tools has been engineered using metal detectable and x-ray visible plastic additives to allow for easy identification of lost parts in the food manufacturing industry. Philip highlighted these products along with its Anti-Microbial range as part of the company’s unique selling point.
Another of the projects that has helped put Hillbrush on the map is the development of its Shadowboards: custom-made visual aids that organise a company’s hygienic equipment according to colour-coded systems, allowing staff to access the right cleaning item for each task, keeps products stored and hung separately to air dry to reduce bacterial growth potential and enables the monitoring of product whereabouts and condition. These boards can be customised to show the company’s and/or its customers’ logo and any other information required. These have been a huge success and reflect the company’s constant endeavours to add value to the customer experience.
Philip explained that Hillbrush is registered to the FEIBP (European Brushware Federation) Charter for Professional Hygiene Brushware, ensuring compliance with all existing hygiene regulations and assuring customers of the product’s fitness for purpose.
Moulding Department
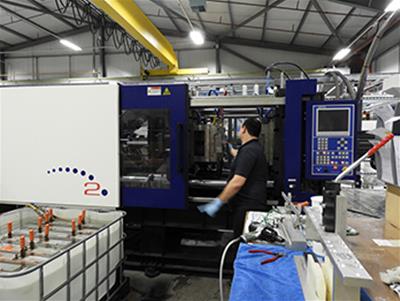
Over the last 3 years, the moulding department has rapidly expanded to accommodate for additional demand; each new moulding machine equipped with its own automatic material feed and dosing system to introduce polymers and additives. The most recent addition has been a new 1000 tonne robotic injection moulding which makes high-speed, large-volume, precision-moulded parts to specific requirements, both in terms of design and composition. So successful is the moulding division that plans are already in place to extend the operation with the addition of further injection moulding machinery in the near future.
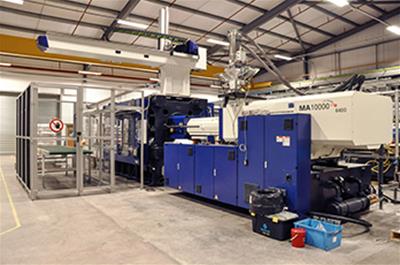
All excess plastic resulting from the injection moulding process is recycled, as it is granulated and re-worked into non-hygiene products.
Philip was keen to highlight that the smooth operation of the whole of the factory is kept on-track with recently deployed state-of-the-art scheduling software and IT systems, which monitor the performance of each machine and each department within the company, supporting the experienced and knowledgeable workforce in their respective functions.
Using its expert knowledge of brush manufacturing, Hillbrush can easily deliver bespoke solutions to meet its customers’ requirements and can advise on the design, materials and all other aspects of the manufacturing process. Logos can be applied to both wood and products with the aid of the in-house printing facilities.
Finally, we were shown the warehousing facilities which employ the latest technology to store, pick, pack and distribute product. This well-organised department ensures that orders are processed and delivered to their various destinations on time!
Moving away from the factory and warehouse, we were shown around the Hillbrush R&D and testing department. With a high emphasis attached to product quality and consistency, this department not only engages the latest engineering tools to design new items, whether standard or bespoke, but also rigorously tests its products using devices such as tuft-pulling equipment, autoclaves and metal detectors.
The Hillbrush team is committed to protecting and preserving the environment and the construction of the new facility afforded the opportunity to re-think its practices and build-in energy and resource saving methodologies. Using recycled materials and, indeed, recycling its own by-products at every stage of the manufacturing process, Hillbrush is making great strides in reducing its ecological footprint.
Everyone knows that a great company relies on great staff and Hillbrush goes that extra mile to ensure that its workforce is well taken care of. With top-notch facilities including a “staff hub” with its own restaurant and rest areas and even a gym, Hillbrush has created a fantastic working environment for its employees, most of whom have been employed for many years, including generations of the same family, reflecting its status as a progressive and caring employer.
Visit Hillbrush!
Having completed our tour, we were excited to be invited to take a closer look at the visitor centre - Visit Hillbrush, with David Hagelthorn joining Philip to show us around. Not only does it benefit from its prime location for catching passing trade, particularly during the summer months as tourists flood into the popular South West of England, but the venture has been successful in also attracting customers from the local area. Many of whom are now regulars in the restaurant which hosts Friday night theme nights with entertainment laid on and has recently been overwhelmed by the interest shown in its Christmas openings which proved immensely popular and were almost immediately sold out!
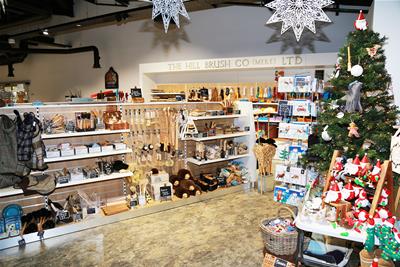
With such a long and well-documented history, the Visit Hillbrush museum really helps the visitor to not only identify with Hillbrush and its roots and company ethos, but also to understand the materials and processed involved in the manufacture of brushware in general.
Guests at the restaurant are surrounded by brushmaking memorabilia, with machinery from a bygone era on display in amongst the tables giving an idea of the effort required to produce brushes, even in days when mechanisation took over many of the mundane tasks that were previously done by hand.
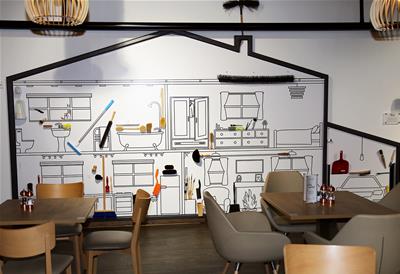
One end of Visit Hillbrush is entirely dedicated to exhibits, both large and small, designed with a very hands-on feel to draw in customers, old and young alike. Walls of photos recording the family’s brushmaking heritage include many gems, among which show our monarch Queen Elizabeth on her visit to the old site in 1952, when current Chairman, Philip Coward, was but a lad. I am sure he behaved appropriately on the day in question and the Queen was left with lasting impression of the company and family; so much so that she is happy for her seal of approval to remain on many of its current products.
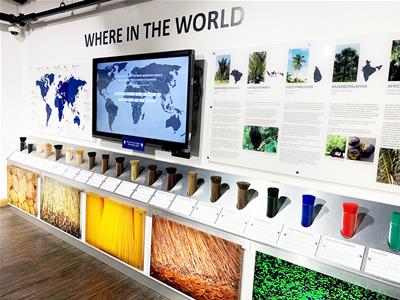
Both Josie and I are very grateful to the Coward family for their generous hospitality and wholehearted commitment to engaging the public in this special industry. Proud of their history, mindful of their present and excited for their future, we are certain that Hillbrush will continue its rise to fame both within the brush world and beyond.
More pictures from our visit can be found in the www.brushexpert.com Image Gallery available via this link.
Brush Expert Visit to Hillbrush






38 Images
Related Articles
What’s Inside the World Brush Expo 2024 Show News
01/07/2024
World Brush Expo News -
Beat the Increase! Reduced Rate for Brush Expert Subscription Before 01 August 2024
17/05/2024
Company News -
Brush Expert 63rd FEIBP Congress Report
17/10/2023
Industry News -
Exhibition "Du Menage a L’Art" Pays a Summer Visit to 2 Prominent French Brush Manufacturers: Brush Expert Reports
06/10/2023
Industry News -
Brush Expert Launches NEW! World Brush Expo Online Resource
07/07/2023
World Brush Expo News -
Reasons Why Paint Rollers Are Often Preferred over Paint Brushes
20/04/2021
Archived -
American Brush Manufacturers Association (ABMA) Annual Convention 2020: Brush Expert Report
08/04/2020
Archived -
National Painting and Decorating Show 2019 – Brush Expert Report
02/12/2019
Archived -
FEIBP Congress 2019 – Lucerne, Switzerland – Brush Expert Report
14/10/2019
Archived -
Brush Expert Visit to Roth Composite Machinery Gmbh for their 100th Anniversary Celebrations
24/09/2019
Archived -
ABMA 2019 Annual Convention Brush Expert Report
11/04/2019
Archived -
Brush Expert visits National Painting and Decorating Show at the Ricoh Arena, Coventry UK
11/12/2018
Archived -
The ABMA 2018 Annual Convention: Brush Expert Report
06/04/2018
Archived -
FEIBP Congress 2016: Brush Expert Report
30/09/2016
Archived -
Brush Expert at Interbrush 2016: A Resounding Success
27/05/2016
Archived -
Brush Expert Launches New Website
19/02/2016
Archived -
57th FEIBP Congress: Brush Expert Report
16/10/2015
Archived -