ZAHORANSKY - New Machines, Systems and Technologies
New products without corners and edges
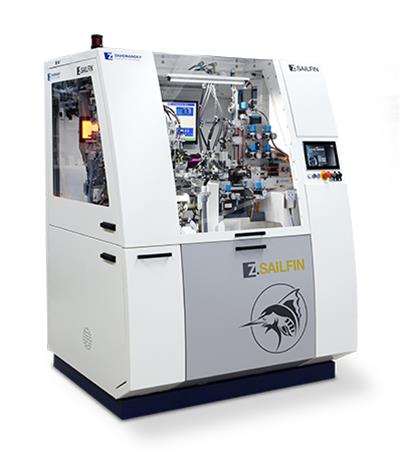
Robert Dous, Head of Sales/Marketing, is looking forward to seeing the reactions of the customers: “It gives us great pleasure to finally be able to show our new machines, systems, and technologies to both the market and our customers. Above all, the modular structure of the CUBE clearly shows our approach to toothbrush production has been logical and well thought out, and that we have been able to implement our ideas on a technical level. In short, all of our new products offer our customers more space in every respect – from the lower space requirement placed on the production hall to the greater potential when it comes to implementing the customer's design ideas, right through to more flexible scaling of the number of units.”
CUBE: the utmost flexibility in the smallest of spaces
The modular basic design of the CUBE allows for toothbrush production with the utmost flexibility and efficiency in the smallest of spaces: in line with the versatile CUBE exhibition system, an equally novel, flexible feeding system for handles made of bulk material will also be showcased. Like the CUBE itself, this feeding units can be scaled accordingly in terms of the number of handles required. Optical camera recognition of the handle shapes ensures easy conversion to other models, which in turn guarantees you flexibility. The handles are inserted via the CUBE Supply Unit into a Carrier Transport System (CTS).
Via the CTS, the handles run through CUBE base units to the individual processing stations like tufting, trimming and final endrounding. There is also the option of integrating additional devices, such as imprinting devices or cameras for quality assurance. The finished toothbrushes are then removed from the CUBE by a robot and placed in the correct alignment on a transport belt. At the end of the belt, the brushes are deposited in a tray for further/final processing in a packaging system such as the Z.PACK.
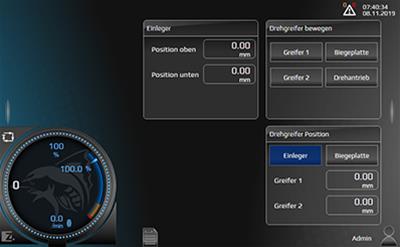
ZMI 4.0: the smart machine controller
The completely re-programed Zahoransky Machine Intelligence (ZMI) 4.0 is now even smarter and geared towards the needs of the worker: with intuitive touch controls, complete with new icons and wizards, it can be used to operate machines fitted with the system (currently CUBE, Z.SAILFIN and Z.LYNX 3) without much training; this is because the programming is based on previously defined modules for specific mechanical movement sequences. By way of example, test users were able to program trimming profiles five to ten minutes faster and thus start the machine five to ten minutes earlier. As part of this process, ZMI 4.0 takes the subsequent operational sequences that should logically follow into account – this helps to minimize operator errors. Should the operator have any questions or be uncertain of anything during operation, the "Help me" wizards are on hand to suggest suitable solutions. The integrated service mode also simplifies international support because it breaks down language barriers, with a unique ID number being present in every field (such as the filament feed settings) on the display. In case of enquiries, the operator only needs to mention this number. This makes it quicker and easier to isolate an error in the event that support is required. In addition to the new operating concept, ZMI 4.0 has also been able to make quicker and more precise actuation times for the servo drives a reality. This is enabling machines such as the Z.SAILFIN to work more quickly and more smoothly, which is reflected in a higher output: instead of the previous 85 brushes, 95 can now be produced per minute. The control center also benefits from greater transparency: the production figures are visualized and can be tracked over certain periods.
Z.LYNX 3: redeveloped for greater performance
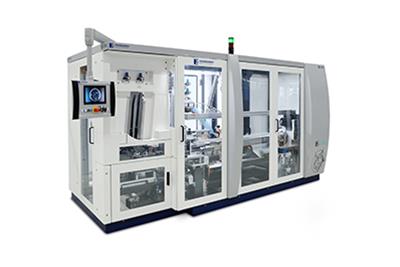
Z.RAY: manufacture wooden toothbrushes precisely and hygienically
Another new product is the Z.RAY, which can be used to produce trendy wooden toothbrushes. To ensure the utmost standards of hygiene, the holes in the handles are drilled in a separate unit and within a protective screen at a rate of up to 800 holes per minute.
Z.PARD: new design improves workplace ergonomics and processes
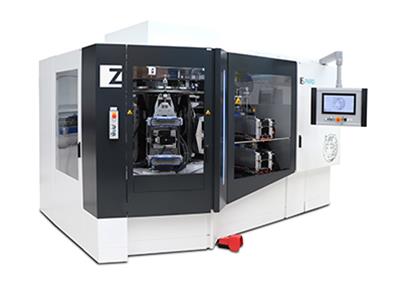
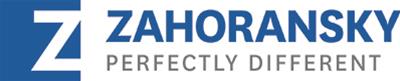
Related Companies
Zahoransky AG
Germany
Zahoransky Moulds & Machines Pvt Ltd
India
Zahoransky Ltd
Japan
ZAHORANSKY SA Unipersonal
Spain
Zahoransky USA Inc.
United States
ZAHORANSKY do Brasil Comércio de Máquinas Ltda.
Brazil
Related Articles
ZAHORANSKY EDGE: High-Tech, Design Freedom and Sustainability in Toothbrush Manufacturing
24/06/2025
Product News -
ZAHORANSKY Machine Portfolio Easy to Retrofit for the Production of Toothbrushes with Plastic Anchor
14/05/2025
Product News -
Change of Executive Board at ZAHORANSKY AG
11/10/2024
Company News -
Heinz Zahoransky Passes Away at the Age of 95
30/08/2024
Company News -
ZAHORANSKY EDGE Enables Efficient Production of Metal-Free Mono-Material Toothbrushes
18/05/2024
Product News -
ZAHORANSKY Sells Mold and Tool Shop in Rothenkirchen
30/01/2024
Company News -
Z.PARD MT for Fully Automated Brush Production
13/11/2023
Product News -
Z.PUMA by ZAHORANSKY: Maximum Performance and Flexibility
06/10/2023
Product News -
The New Z.SCORP from ZAHORANSKY
12/07/2023
Product News -
A Mono-Material Toothbrush by ZAHORANSKY and Evonik
06/03/2023
Archived -
New ZAHORANSKY Microsite Provides an Overview of the Latest Medical Technology Solutions
26/01/2023
Archived -
ZAHORANSKY and KOCH Pac-Systeme Establish Close Cooperation in the Blister Packaging Sector
02/11/2022
Archived -
ZAHORANSKY Introduces Expanded Management Team in India
26/07/2022
Archived -
ZAHORANSKY Repositions Sales and Marketing
02/02/2022
Archived -
ZAHORANSKY Bids Farewell to Interbrush - New Formats for Personal Exchange
07/12/2021
Archived -
ZAHORANSKY Introduces New Apps for Contactless Support and Direct Spare Parts Orders
16/03/2021
Archived -
ZAHORANSKY Group Acquires Dialysis Division of FLG Medizintechnik GmbH
18/01/2021
Archived -
ZPARE – New Application by ZAHORANSKY
17/11/2020
Archived -
ZAHORANSKY Z.PARD: Reworked Design for Optimized Operating and Production Processes
02/11/2020
Archived -
New Micro-Injection Mold Produces Toothbrush Tips for the Z.VAMP from ZAHORANSKY AG
11/09/2020
Archived -
ZOLVE – New Application by ZAHORANSKY
27/08/2020
Archived -
Dr. Bernd Stein to Become New Chief Technical Officer at ZAHORANSKY AG
31/07/2020
Archived -
Z.RAY: For the Precise and Hygienic Manufacture of Wooden Toothbrushes
10/07/2020
Archived -
ZAHORANSKY Receives Large Order for Systems for the Processing of Vaccine Containers
10/07/2020
Archived -
New ZAHORANSKY Customer Magazine
26/06/2020
Archived -
ZAHORANSKY Improves Output and Operating Comfort in Twisted-in-Wire Brushes with New Lines and Improved Machine Controls
25/06/2020
Archived -
ZAHORANSKY Newsboard – Update
21/04/2020
Archived -
Record Figures for ZAHORANSKY: 2019 is the Best Year in the Company History
15/04/2020
Archived -
ZAHORANSKY Launches Newsboard with Comprehensive Information Regarding Current Developments During Coronavirus Crisis
01/04/2020
Archived -
Zahoransky USA Deemed Essential Business
27/03/2020
Archived -
ZAHORANSKY Brush and Broom Machines for Hygienic Measures
03/03/2020
Archived -
Z.SHARK Family of High-Performance Tufting Machines Now Optionally Available with Double Turret
10/02/2020
Archived -
ZAHORANSKY: Future-Proofing “Black Forest Quality” Made in India
13/12/2019
Archived -
Z.PACK 6 | 8 | 11 from ZAHORANSKY: The Competition Can Pack it All Up
12/10/2019
Archived -
Environmental Management at ZAHORANSKY
11/10/2019
Archived -
ZAHORANSKY at K 2019: The Z factor is Included
23/09/2019
Archived -
ZAHORANSKY Has Received Several Awards
01/08/2019
Archived -
Winfried Ebner to become third Board Member at ZAHORANSKY AG
26/03/2019
Archived -
Happy Birthday Dr. Heinz Zahoransky!
10/09/2018
Archived -
ZAHORANSKY USA Open House 2018
12/07/2018
Archived -
ZAHORANSKY receives the "Innovation Award 2018"
29/06/2018
Archived -
Beef Up Your New Z.LION from ZAHORANSKY - The King of the Brush & Broom Production Jungle
23/05/2018
Archived -
Visit ZAHORANSKY at Plastpol 2018 - The 21st International Fair of Plastics and Rubber
09/05/2018
Archived -
Visit ZAHORANSKY at the NPE Show
06/04/2018
Archived -
ZAHORANSKY: Introducing Our Beastly New Website.
13/03/2018
Archived -
Power for Your Brush Production: Z.LION from ZAHORANSKY
28/02/2018
Archived -
High-Tech Solutions for your Personal Care Products from ZAHORANSKY
17/02/2018
Archived -
ZAHORANSKY Rises for the Fourth Time in a Row
06/02/2018
Archived -
ZAHORANSKY – Where the Future is at Home
13/10/2017
Product News -
ZAHORANSKY Achieves Highest Order Intake in Company's History
05/09/2017
Archived -
ZAHORANSKY USA Inc. Change in Management and Service Technician
03/08/2017
Archived -
Next Generation of Brush Production: Zahoransky's Z.LION
19/07/2017
Archived -
ZAHORANSKY: Ideas Make the Difference
19/07/2017
Archived -
Visit Zahoransky At Chinaplas 2017!
04/05/2017
Archived -
ZAHORANSKY given the 2016 MSG Award
18/04/2017
Archived -
Zahoransky Looks Forward to Celebrating 100 Years at the ABMA Convention
15/03/2017
Archived -
ZAHORANSKY Automation & Molds and Packaging
17/02/2017
Archived -
ZAHORANSKY joins Forces of Sales & Service in Shanghai
03/02/2017
Archived -
ZAHORANSKY Continues Upswing Thanks to Strong Demand
03/02/2017
Archived -
Inauguration of ZAHORANSKY’S New Plant in Spain
25/10/2016
Archived -
Z.PARD from ZAHORANSKY
01/09/2016
Archived -
Zahoransky Brings a Black Forest Feeling to Interbrush
26/05/2016
Archived -
Welcome to ZAHORANSKY – Where the Future is at Home
22/04/2016
Archived -
Zahoransky do Brazil
21/04/2016
Archived -
Production of High Quality Toothbrushes on a Milacron Injection Molding Machine
20/04/2016
Archived -
ZAHORANKSY Set to Attend the ABMA Convention 2016
26/02/2016
Archived -
Continuous and solid growth of ZAHORANSKY GROUP
28/01/2016
Archived -
ZAHORANSKY Receives (Re)certification
30/10/2015
Archived -
ZAHORANSKY Booth Party
20/10/2015
Archived -